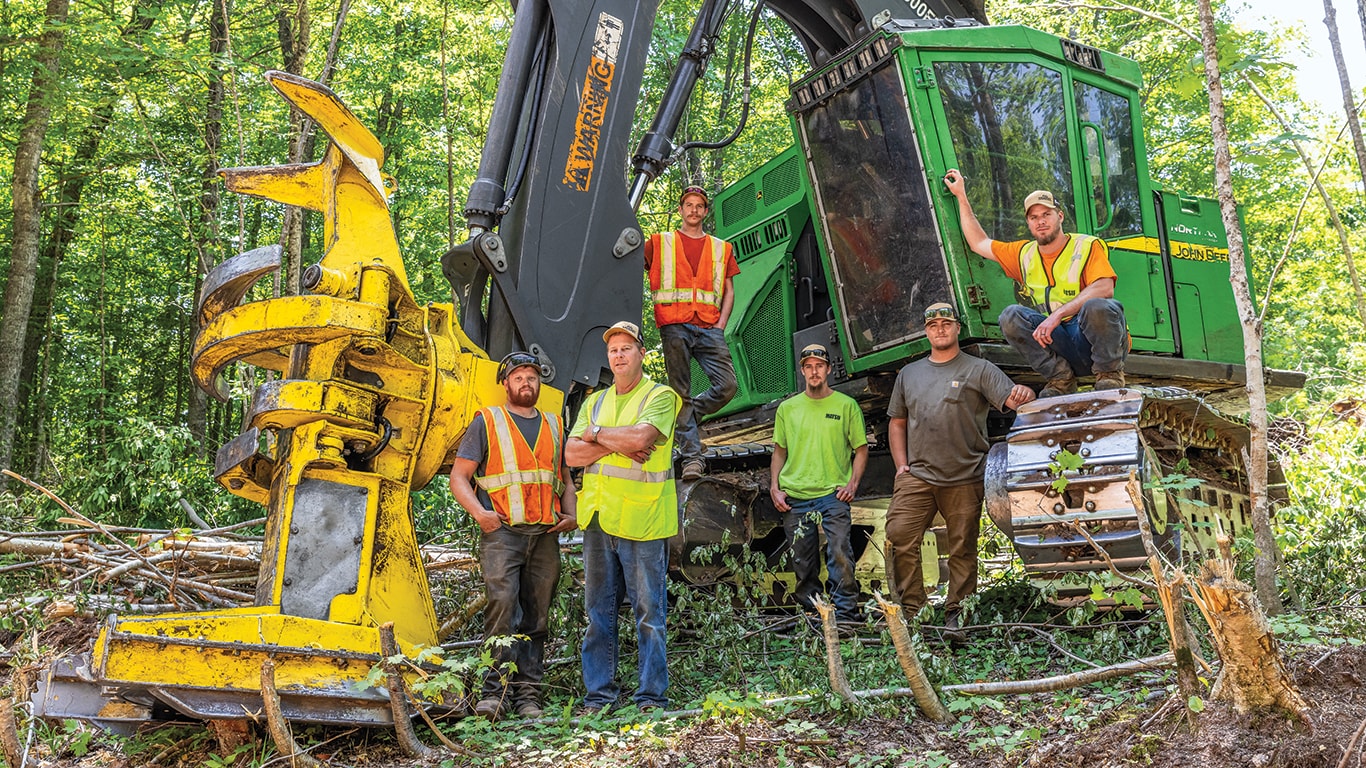
Max Tervo, Doug Anderson, Ladd Anderson, Nash Anderson, Eli Larson, and Dane Anderson, all of Doug Anderson Logging, stand beside a John Deere 853M Tracked Feller Buncher.
Fall 2023
Front Man
Michigan logger Doug Anderson sings the praises of teamwork and a hybrid logging system
8 MIN READ
Logging is often generational. But Doug Anderson, owner of Doug Anderson Logging, Calumet, Michigan, never pressured his sons to enter the family business. “I never told my boys they had to come work with me,” he says. “I wanted them to find their own way because there are easier ways to make a living.”
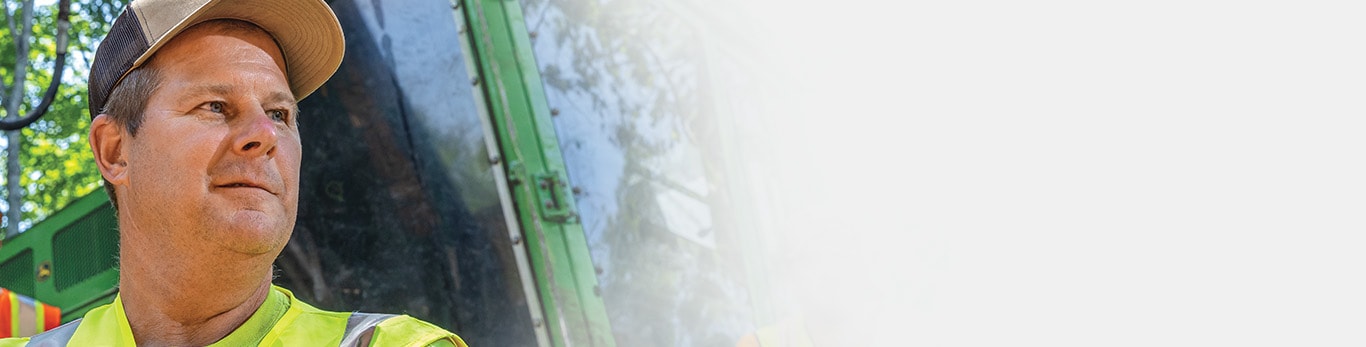
“I love being outside and being my own boss.”
Two of Anderson’s sons trained to work in other fields, but four decided to log with him in Michigan’s Upper Peninsula. His son Dane runs the company’s John Deere 853M Tracked Feller Buncher. Another son, Nash, runs one of the two Deere 1210G Forwarders. Anderson’s youngest son Ladd runs the Deere 803MH Tracked Harvester. And his son Soren owns his own log truck and hauls wood for the company. “I’m proud they’re all doing a great job,” he says.
Anderson’s own father encouraged him to get an education and find a career. “He told me he knew I’m going to do what I’m going to do. But if I wanted to work for him, he’d hire me.” Anderson has never regretted the decision. “I love being outside and being my own boss.”
Anderson grew up in Boston, Michigan, not far from the company’s shop in Calumet. His father started a logging company in the early 1960s. During the summers when he was growing up, Anderson would carry his father’s oil and gas jugs for the chainsaw. “I was a gopher,” says Anderson. As he got older, he learned to run the chain saw and cable skidder.
In 1993, Anderson bought his father’s three skidders and a bulldozer. In 1997 Doug Anderson Logging purchased its first feller buncher, and in 1998 the company bought a new John Deere grapple skidder. “I made one skid with it and knew it was made for skidding,” he remembers. “To move a lot of wood, we realized we needed a grapple so the operator wouldn’t have to get out of the cab all the time and hook up a cable.”
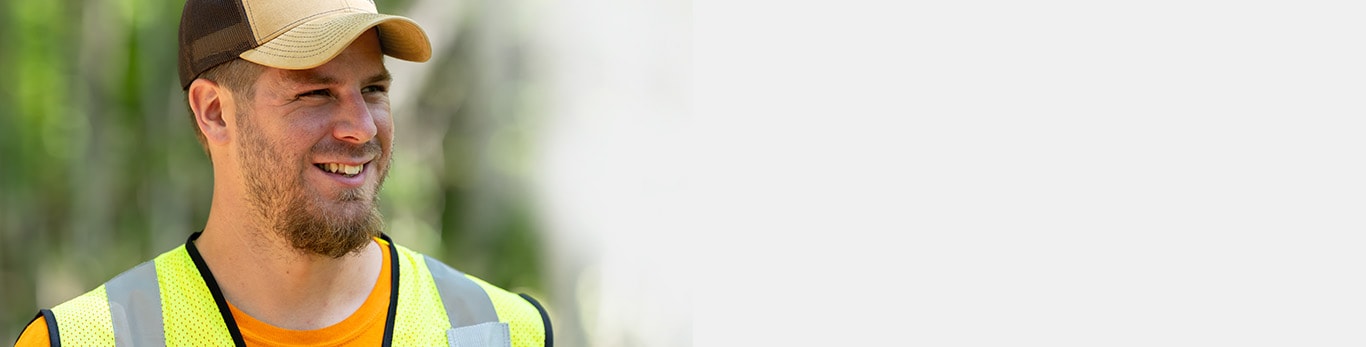
“The feller buncher keeps things flowing. We’re able to keep two forwarders busy. There’s a lot more wood in the bigger piles.”
Never say never
Like his father, Dane has always loved the outdoors, but he wasn’t sure if logging was his calling. “Running a chainsaw all day was fun and kept me in shape, but it was hard work. I wasn’t sure I wanted to do it as a career,” he recalls.
Then at the 2015 Oregon Logging Conference, Dane saw videos of forwarders and processors. “It just made everything easier,” he recalls. “Dad mentioned the possibility of going to cut-to-length, and it became a dream of mine.”
Around this time, many loggers in the Upper Peninsula were switching over to cut-to-length. Doug had purchased a used processor and saw the potential of running it behind his feller buncher. “I made up my mind to go to cut-to-length and bought a new John Deere forwarder and processor as well as a tracked feller buncher.”
Not a lot of companies in his region run a hybrid system with a feller buncher cutting out in front of a processor. But Doug prefers to run a feller buncher instead of a harvester for felling wood. “We get a lot more production that way,” he says. “Because it’s tracked, it’s more stable and can handle a bigger head. The hot saw cuts down trees faster. Plus, with a feller buncher, you don’t have to sharpen chains all the time, and you’re not bending bars.”
The feller buncher can fell directionally so that the crew can create larger piles for skidding. “A harvester can only create small piles,” explains Doug. “It’s more efficient to have it sort and process the piles, so when the forwarder goes in, it comes out with a full load. I know another logger in my area who said he’d never go with this type of system, but he just bought a buncher. So never say never.”
“The feller buncher just keeps things flowing,” adds Dane. “We’re able to keep two forwarders busy. There’s a lot more wood in the bigger piles, so it’s fast forwarding.”
The logging operation produces six to seven loads of “Michigan” double trailers daily or roughly 20 to 24 cords per truckload. About 95 percent of the wood is hardwood, most of which is oak, along with maple, birch, basswood, and ash. About 80 percent is used for pulp, with the rest used for logs.
The crew is currently working on a 250-acre site near Twin Lakes, Michigan. Logging in the Upper Peninsula is always challenging. The site is typical, with rocky, hilly terrain and big timber.
“The tracked 803MH and 853M work really well in this terrain and in the big trees,” says Dane. “They just stick to the hills.”
The 803MH is the Andersons’ third processor. The larger platform and the highly capable Waratah HTH623C Harvester Head help harvest the big wood. “The 623 is a little bigger than our 622 Heads, so it has more power to knock branches off of the big trees,” says Doug.
The big picture
Having the right mix of the right-sized machines has been key to maximizing production. But teamwork is critical. “It doesn’t matter how many trees you can cut if the next guy comes through and can’t deal with the wood because it’s crisscrossed,” explains Doug. “You need to set it up so the next guy’s job is easier. The buncher needs to leave a neat pile for the processor, and the processor needs to sort wood, so the forwarder doesn’t have to pick through a bunch of sticks. Instead of every man for themselves, you need to look at the big picture. If everybody focuses on making everyone else’s job easier, production will come.”
Having TimberMatic™ Maps, John Deere’s map-based production-planning and -tracking system, on the processor and forwarders also helps optimize production. “It’s really handy, especially for the terrain we cut, and it removes a lot of the guesswork,” says Dane. “If a crib trailer shows up and needs a load of pulp, the operators can see right on the map where everything is at. Operators can identify and share the best skidding routes with each other, so no one is just blindly driving around. It’s just very efficient.”
Dane appreciates other Deere technology solutions. Intuitive and accurate Intelligent Boom Control (IBC) on forwarders, for example, makes it easier to control boom movements compared to forwarders not equipped with IBC. “I can go six months without running a forwarder, and with IBC, I can get up to speed quickly,” says Dane. “Deere keeps up with technology, and they build reliable machines. They just go and go.”
The local John Deere dealer, McCoy Construction & Forestry, uses JDLink™ to remotely monitor the company’s machines so they can alert the Andersons proactively if there is an issue. Service and support have been excellent, according to Dane: “They’ve been awesome to deal with. We can resolve simple issues over the phone, and they almost always have the parts we need in stock.”
All for one
Two years ago, Dane began gradually buying out the logging business from his father, so Doug can focus on roadbuilding. Dane currently owns the 853M Tracked Feller Buncher and 803MH Tracked Harvester, and he will also purchase the forwarders. “Things are rolling along as planned,” says Dane. “I didn’t want to take on everything at once.”
Doug’s son-in-law, Max Tervo, will be buying Doug’s three logging trucks and managing that part of the operation. “I’ll be backing everyone by doing roadbuilding and snow removal, but I probably won’t change my company name,” says Doug. Logging, after all, is what has brought the Anderson family together.
“We all get along really well,” says Dane. “Everyone is very easygoing. I’m happy we see eye to eye and have been able to make this company what it is. And I’m excited about what we will accomplish in the future.”
Doug Anderson Logging Inc. and Dane Anderson Logging LLC are serviced by McCoy Construction & Forestry, Escanaba and Marquette, Michigan.
Related Articles
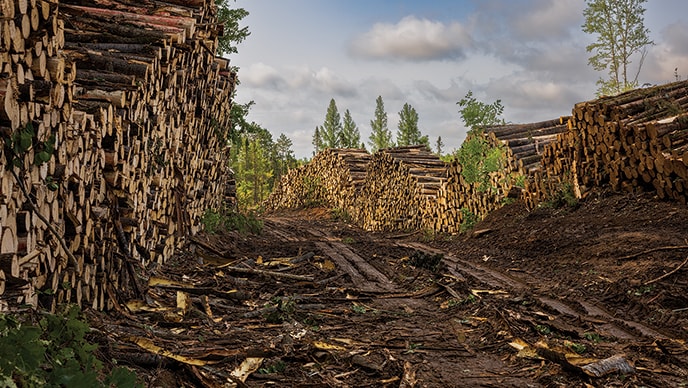
The Marshall Plan
Marshall Logging continues eight decades of logging by adapting to change and adopting new technology.
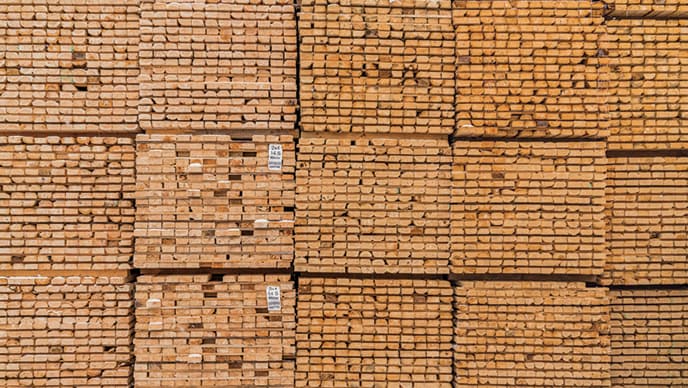
Growing Tall
A&A Brochu Logging has used vertical integration and economies of scale to gain an edge.
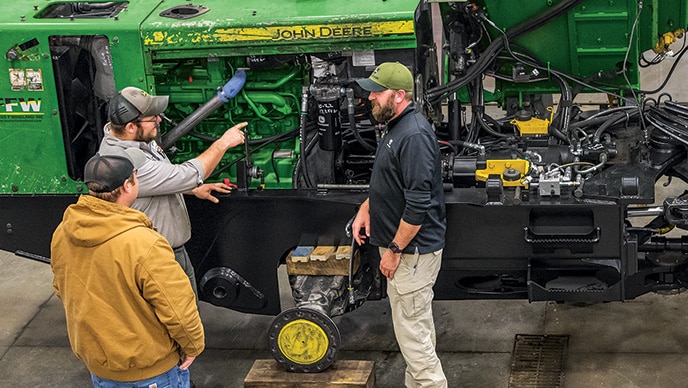
Second Wind
The John Deere Powertrain ReLife Plus program extends the life of skidders while helping loggers manage costs.
Do you think your company's story would resonate with others in the logging industry?
SHARE YOUR JOURNEY