Agriculture, Livestock/Poultry December 01, 2022
Fast Feed
.
Ingenious self-serve bar streamlines winter feeding.
Feeding cattle in the winter can be tough in much of the U.S. and Canada—tough on producers, tough on the land, and tough on the wallet. That goes double for livestock producers who have off-farm jobs and end up feeding on cold, wet nights and weekends.
"It's in wintertime when we tear our farms to pieces," notes Dr. Steve Higgins, director of animal and environmental compliance at the University of Kentucky.
Higgins has made it his mission to help producers be gentler on their land and on themselves. One of his recent innovations is a large-bale feeding system that limits hay handling and lets the cattle do most of the work.
Higgins and farm superintendent Dan Miller constructed two of the systems at Eden Shale Farm, a 961-acre demonstration farm near Owenton, Kentucky, operated by the Kentucky Beef Network.
One of the feeders is a retrofit of an old tobacco barn. The other was built from scratch with a sloped concrete floor under a fabric tunnel. With a full load of 30 to 32 bales, each feeder can sustain a herd of 25 head—about the Kentucky state average—for a month.
The principle is simple. Think of it like a magazine in a pistol, with the bales lined up like bullets. Instead of a spring pushing the rounds into the pistol's chamber, the cows push a roller-mounted gate into the bales. The animals are the spring, and they push forward as they eat the hay.
Above. At Eden Shale Farm, the Kentucky Beef Network runs small herds to stay in step with the state's producers. Steve Higgins is all about efficiency. The 22-foot gate in the built-from-scratch feeder accommodates one-third of a 25-head herd at a time. The wooden gate in the barn alley feeder moves on barn door rollers.
Keep it simple. Higgins is all about making things simple.
Most livestock producers harvest forage, bale it, and move the bales to storage. Then they pull the bales out of storage in the winter and deliver them to the herd. That's a lot of driving, a lot of fuel, a lot of climbing in and out of the cab opening and closing gates. And it's compacting soil when it's wet and vulnerable.
"We used to move bales and rings to 40 different places," he notes. "Now we move that hay one time. Once we peel off the strings, this barn is ready to feed."
That adds up to a huge savings.
"It costs us $10 a bale—$20 a ton—to put this in the barn," Higgins says. "[Usually, farmers will] spend $80 a ton driving hay around the farm."
At both feeders, cows have 24/7 access to hay and free choice minerals. To access water, they have to walk 150 feet around a fence.
"If you have food and water in the same place in the operation, you have no reason for the animal to leave," Higgins notes. "After they eat, I want to motivate them to get a drink of water."
Miller says the system keeps the feeding area clear—and clean.
"They'll come in here and eat, they'll get a drink, then they'll disperse out in the woods," Miller points out. "They're cleaning that hay up, and the manure load is not that high because they aren't spending a lot of time here. If there was water here, they would be loafing."
Clever design. Higgins' feeder designs are available free online at edenshalefarm.com under the Producer Resources tab. In all, the built-from-scratch feeder cost about $15,000, and retrofitting the barn cost $3,600.
Both systems are packed full of high-efficiency features.
The feeding area of the tunnel-covered feeder opens to the south so the sun melts ice and dries moisture on the concrete floor, which slopes down to either side to keep the forage dry.
The gates in that unit run on caster wheels locked by a slide onto a 2x2 steel tubing rail so the cattle can't derail the rack. Though the rack and easy-to-replace feed panels weigh 1,200 pounds, the system is so well balanced a breeze can push it.
In the barn alley feeder, Higgins constructed a wooden gate with barn door rollers and tracks.
In both units, the racks are built as 22-inch-deep frames so cows have to reach for the bales and clean up fallen hay, cutting waste.
"Last year, the amount of waste from this system wouldn't fill the back of a pickup," Higgins says.
Miller says the tunnel-covered feeder quickly became his favorite place on the farm.
"Last year, we fed 30 head for 50 days without doing anything other than checking on them," the superintendent says. "No effort, no starting the tractor, no bringing them anything extra."
It's as simple as that. ‡
Read More
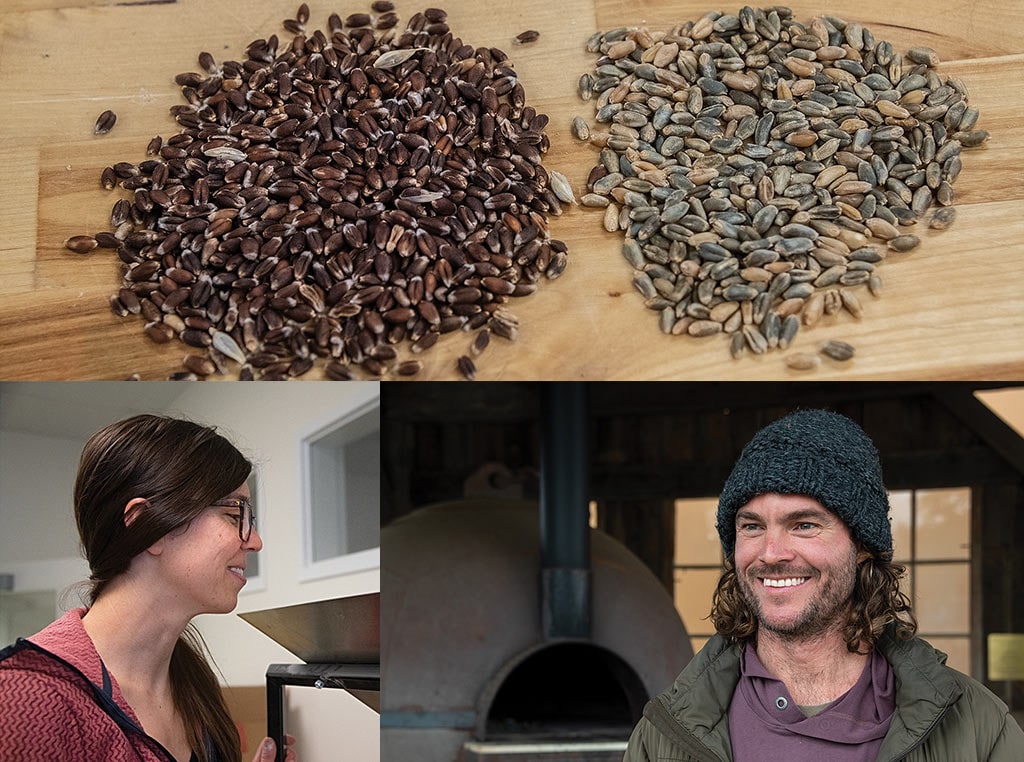
AGRICULTURE, EDUCATION
Small Grains, Big Questions
WSU Breadlab researchers tackle opportunities for cereals.
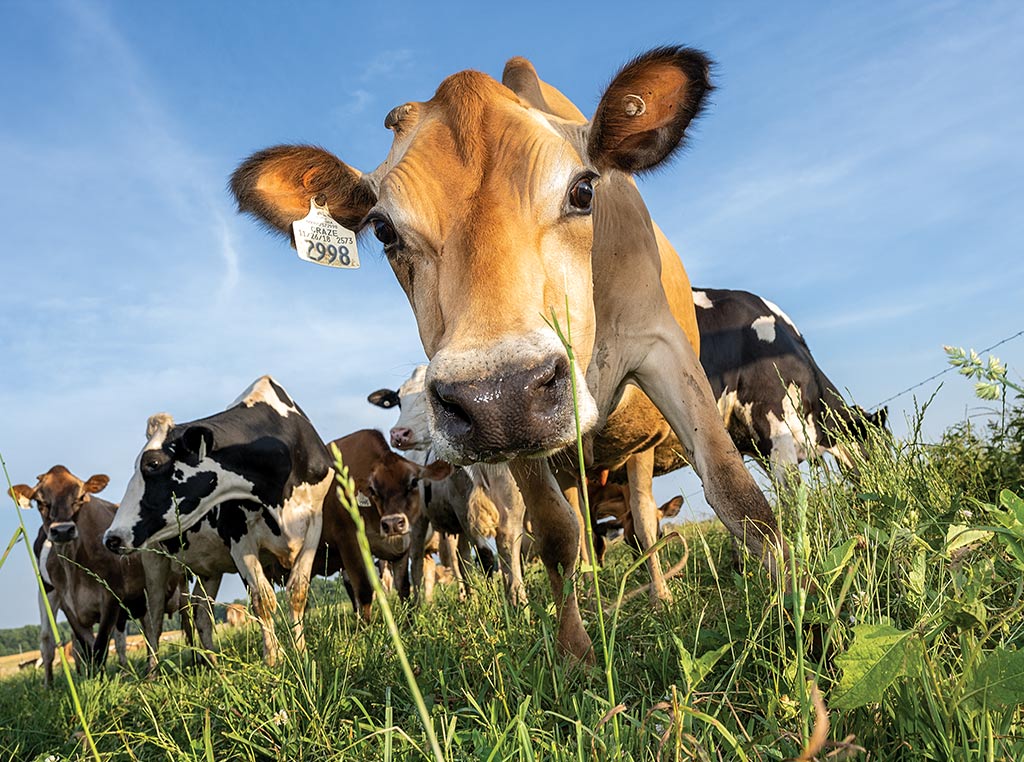
AGRICULTURE, FARM OPERATION
Bottling Success
Starting a unique bottling facility stabilized farm.