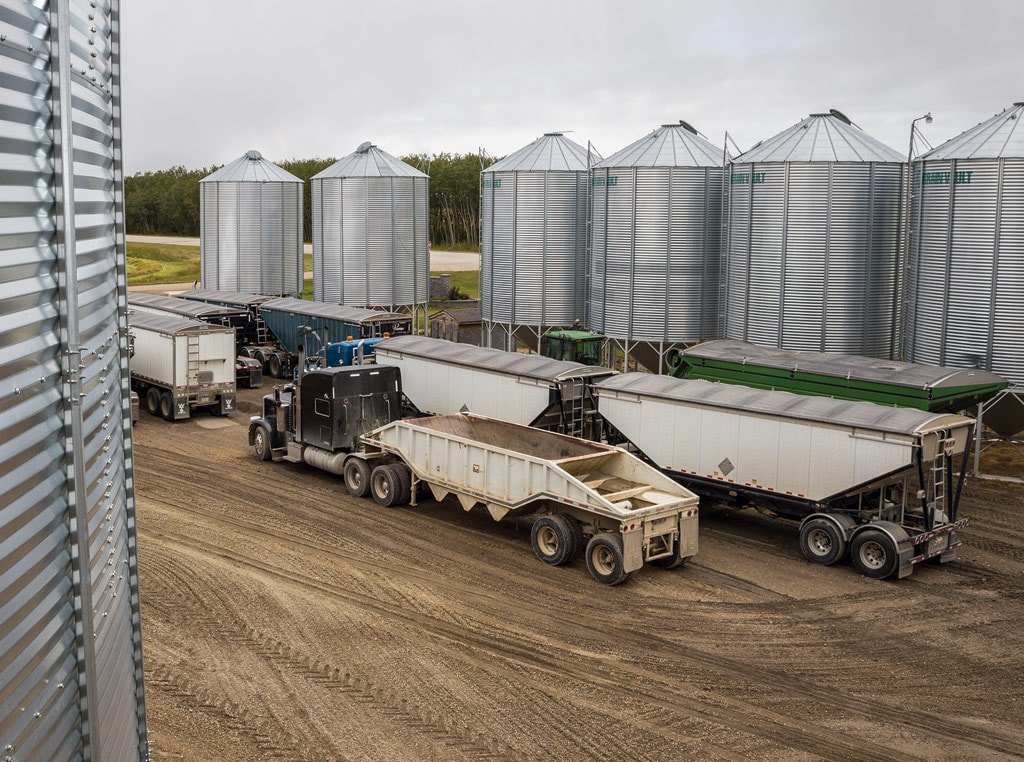
There are benefits to being able to load trucks rain or shine, Winny says. So they improved their binyard’s drainage and hauled in lots of gravel and crushed rock.
Agriculture, Farm Operation February 01, 2021
Building a Binyard
Rethink on-farm storage with an eye to the future.
Having adequate grain storage has long played an important role in grain marketing. Prices typically are at their lowest during harvest so having storage capacity provides producers with flexibility to capture any premiums that pop up later in the crop year. But as farms have grown larger, and yields have increased, many farmers are rethinking where they should locate their binyards.
“While it sounds self-serving, I advise anyone thinking of building to start by talking to a grain management expert,” says Lyle Muyres, Vice-President of marketing at Corr Grain Systems in Humboldt, Saskatchewan. “They’ve seen the good and the bad over time and can offer good advice.”
Large centralized bin sites have many benefits, but you do lose some harvest flexibility, Muyres says. That’s why many large farms use grain bags for temporary in-field storage during harvest. Farmers can either market it or move it into long term storage over the winter months.
Size of operation is always a consideration when choosing a bin site. A farm that only hauls out a few truckloads now and then has very different needs from one that has to maintain continuous grain flows throughout the year. Modern binyards are designed with straight rows on well-drained sites; enough open space is left at each end so a semi or a super B-train can easily turn around.
Five key points. If you are choosing a site for a central grain handling facility for a large farm there are five fundamental points to consider, Muyres says. First ensure that it’s located on a primary road, or as close to one as possible, to avoid road weight restrictions. Second, ensure it has access to the natural gas capacity you need to run your grain dryers or factor in the cost of propane. Third, make sure it has the electrical service you need. If you are intending to build one with high-capacity legs or a pneumatic grain handling system you’ll need three-phase power or be able to bring it in at a reasonable cost. Fourth, choose a site with good cellular service, so you can monitor and manage your grain with your cellphone no matter where you are. Finally, leave room for future expansion.
Grain storage was a big consideration for Kurt and Jim Winny when they purchased an 11,000 acre farm at Garrick, Saskatchewan in 2016. Their initial purchase came with just over 400-thousand bushels of storage with inline grain drying capacity and was located adjacent to the region’s major highway. They also bought shares in the local Torch River Shortline railway.
“A primary highway was important because we can get real premiums if we can haul grain when others can’t,” Kurt Winny says. “Being able to load trucks rain or shine has real benefits, so we upgraded the site with a few drainage projects and brought in a lot of gravel and crushed rock.”
The site met their initial needs, but it became too small once they picked up an additional 7000 acres of land. Their region typically has a tight harvest window so added grain drying capacity was critical too. The Winnys settled on the site of a former Saskatchewan Wheat Pool grain elevator in the nearby village of Choiceland. Despite having to tear down the old wooden annexes and replace them with 200,000 bushels of steel bins to be insurable, the site had lots going for it.
“It’s located on both a primary highway and the Torch River Rail way,” Kurt Winny says. “This allows us to ship using two modes of transportation. The site had full 600-volt three phase power and a 19-million BTU natural gas line that once served an alfalfa dehydration plant that used to be located in the town. We have access to all the natural gas for drying we need.”
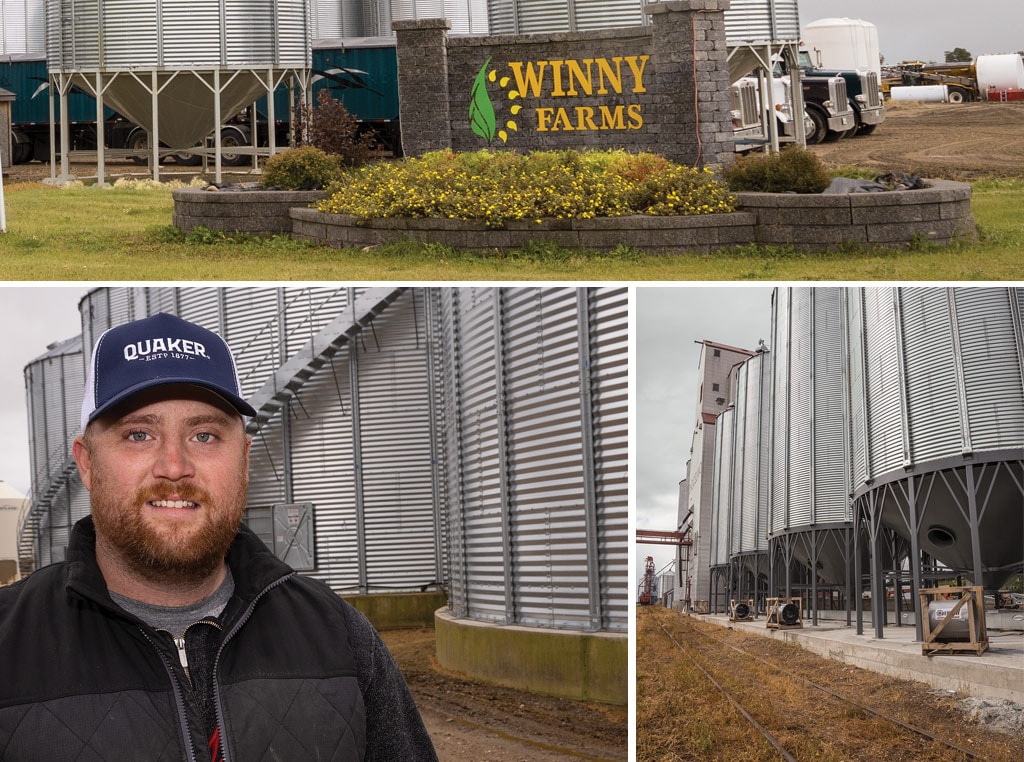
When it became too small they purchased a former grain elevator along the shortline railway and added a dryer and 200,000 bushels of wet storage.
“That’s important because many farms can’t get natural gas in the quantities they need once it gets cold,” Muyres says. “It’s worthwhile to talk to your utility to see what’s available where; the answer might be a reason to choose one site over another. If you can’t get the volume you need, you’ll have to look at propane.”
The type of electrical service that’s available is another consideration. Ninety percent of farms Muyres works with only have single phase electricity. This works for many designs, but if you’re planning to have a highly automated high-capacity leg or pneumatic system, finding a location with access to three phase service is essential.
“Security is another advantage for having a centralized binyard that operates on electricity,” Muyres says. “Few people think about it, but as long as you can cut power to the site when you leave, no one will be able to steal grain from your bins.”
“We knew what we wanted when we chose this place,” says Jim Winny. “It has everything we were looking for; primary road and rail access, three phase power and a high-capacity natural gas line. We’ll know after we’ve used it for a while if we overlooked anything.”
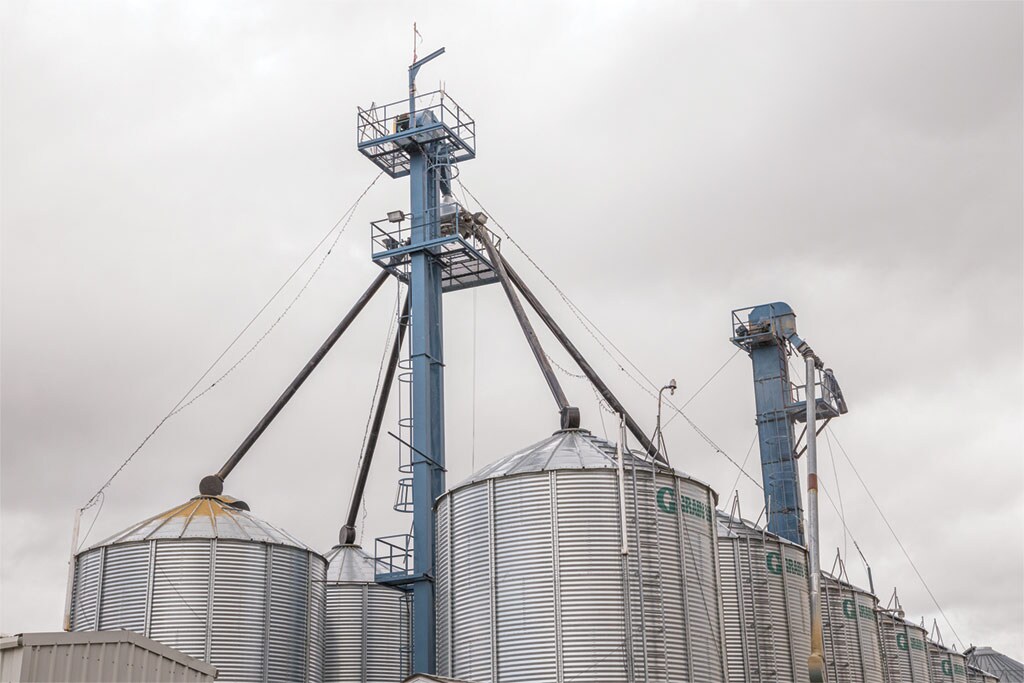
An ideal central grain handling facility should be located on a primary highway, access to an adequate natural gas supply, three phase electricity, good cell phone service & have room for expansion
Read More
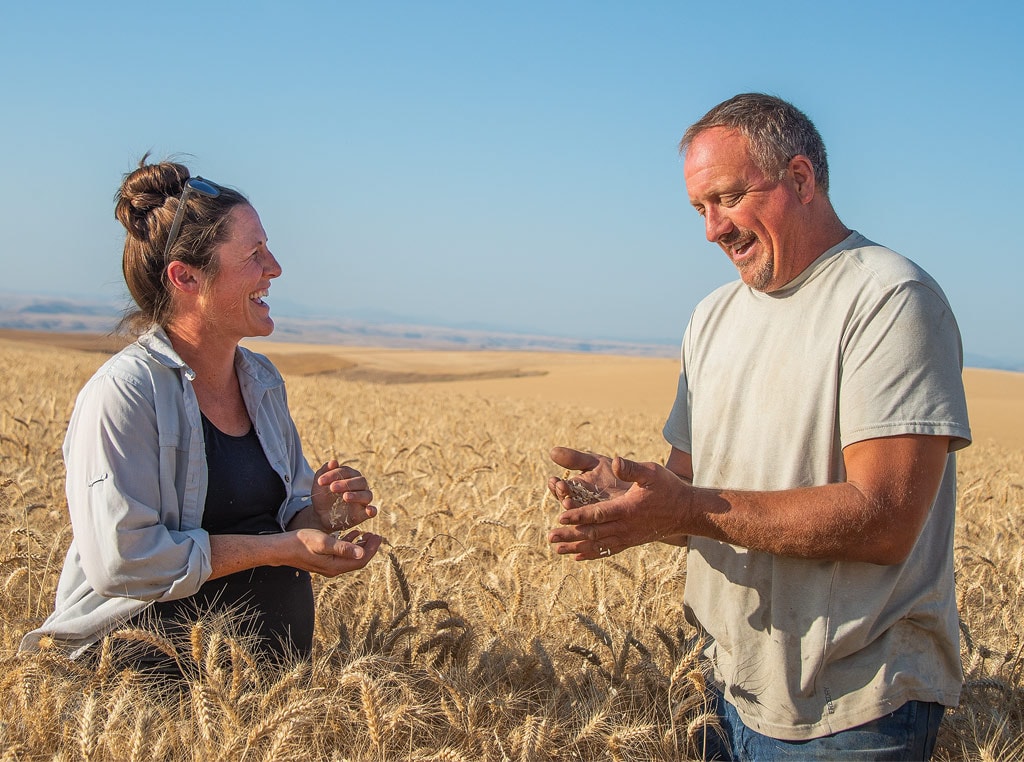
Ag Tech, Farm Operation
DIgging Into Data
Refining knowledge to farm successfully in a margin era
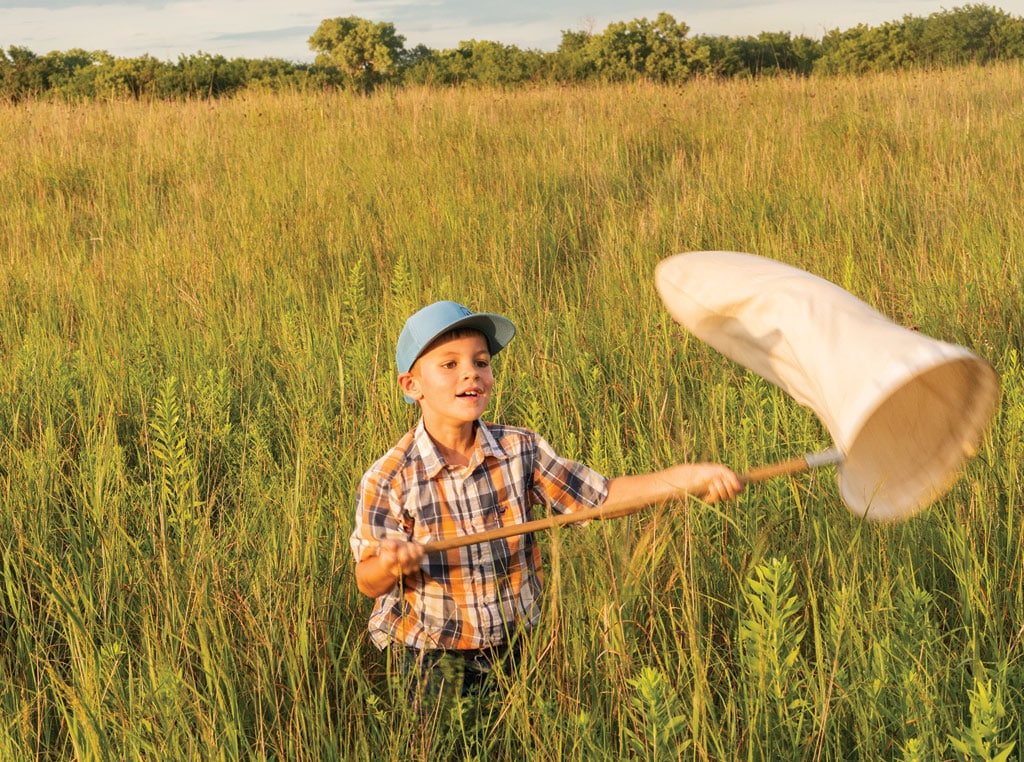
Agriculture, Sustainability
Insect Inventory
Declining numbers are bad news for agriculture.