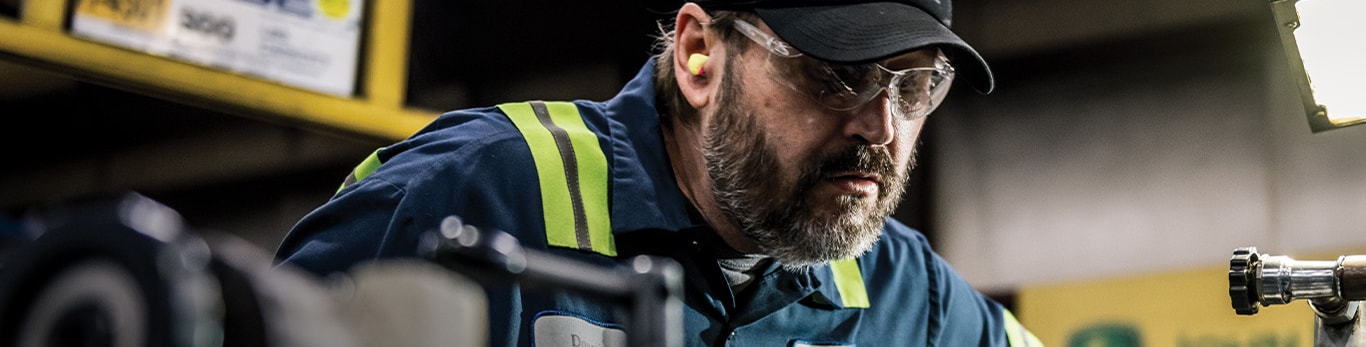
In today's environment of tight margins and labor constraints, there is no room for downtime, especially when it comes to the equipment a customer's livelihood depends on. When an important part breaks down or wears out, customers need a quick, quality solution to get them back on the job.
One solution that is becoming increasingly important in the off-highway equipment industry is remanufactured parts and components. Remanufacturing is a comprehensive industrial process that returns a worn-down or failed part to like-new quality.
John Deere Reman is the remanufacturing division of John Deere and provides customers with genuine, lower-cost remanufactured parts that deliver the same level of performance and reliability as new components. Remanufactured components available from John Deere include engines, engine components, hydraulics, drivetrain components, and electronics components.
John Deere Reman helped John Deere customer St. Louis Composting save money and avoid downtime when the company noticed that its PE6068TF275 6.8L industrial diesel engine was running rough.
A same-day solution
St. Louis Composting is the largest compost producer in the St. Louis metropolitan area. The company oversees seven composting facilities that process over a million cubic yards of green material annually — more than one-third of all yard waste generated in St. Louis County.
In addition to composting yard trimmings gathered by the area's major waste haulers, St. Louis Composting receives and composts other material collected from landscapers and homeowners. The company also transports and processes more than 500 tons of organic food waste each week.
With an operation this large, St. Louis Composting relies heavily on its equipment to keep things running smoothly. So when the company noticed that one of its mulching machines was backed up, it called in John Deere distributor CK Power for help.
CK Power dispatched a John Deere-certified technician to diagnose what was wrong with the machine and its industrial engine. The technician determined that the engine's fuel injectors and fuel injection pump needed to be replaced.
Working with the CK Power parts department, the technician located John Deere remanufactured fuel injectors and an injection pump that the parts department had in stock. (CK Power works with the John Deere Parts Distribution Center in Milan, Illinois, to source parts.)
The service technician was able to return to the site, install the injectors and pump, and get the mulching machine back up and running — all on the same day the service request came in. Not only did the use of Reman parts help get St. Louis Composting operational again within just a few hours, but it also helped save the company money.
"We've had great success using John Deere Reman parts," says David Garett, service manager for the St. Louis CK Power branch. "In our line of business, our customers are all about getting their equipment back to operational use. So when you can also provide them with cost savings and help to get them back up and running quickly, it really helps bolster our relationship."
Reman: Another tool in the toolbox
Reman is another tool in both a distributor's and customer's toolbox.
Using Reman parts helps to minimize downtime and get the customer back to work sooner while costing less — typically 30% less — than purchasing a new component.
All John Deere Reman parts and components are inspected and 100% dynamically tested to original performance criteria. Customers who opt for John Deere Reman products can run their equipment with confidence knowing that these parts deliver the same quality and performance as new parts and are backed by a one-year, unlimited-hour parts warranty, including labor if installed by an authorized John Deere distributor or dealer.
"We take pride in getting our customers back up and running in a short time. The parts availability with John Deere Reman is great as well and so is the price point we're able to offer our customers," Garett says. "With the warranty offered on Reman parts, almost every one of our customers is just fine using a Reman part."
We've had great success using John Deere Reman parts. In our line of business, our customers are all about getting their equipment back to operational use. So when you can also provide them with cost savings and help to get them back up and running quickly, it really helps bolster our relationship.