Investments at John Deere Harvester Works
The People and Processes Behind the X9 Combine
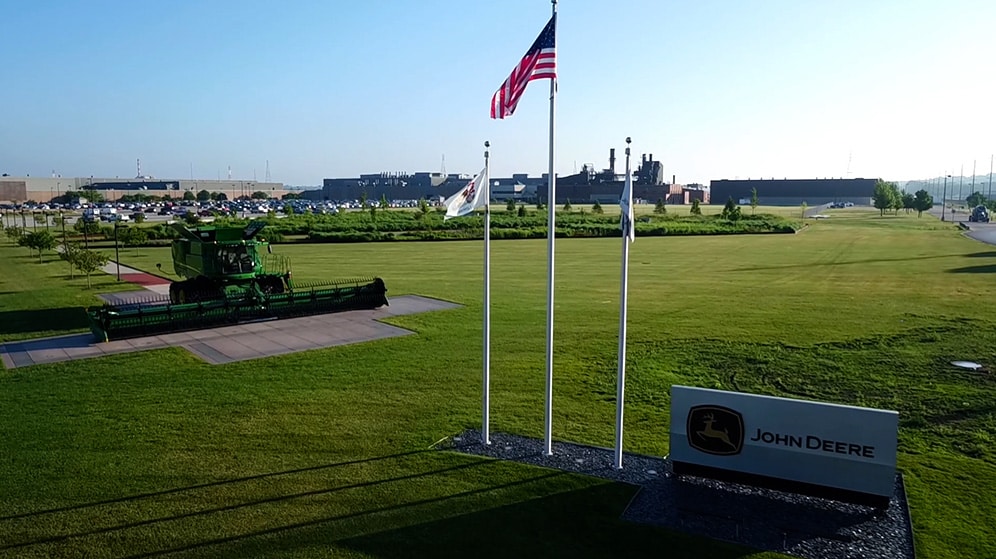
John Deere Harvester Works factory in East Moline, IL
Since 1912, Harvester Works has been home to the people who assemble John Deere combines and front-end equipment. Generations of skilled team members in East Moline, Illinois, have poured their experience and craftsmanship into every machine. Some have been doing it for over 50 years—and it shows!
“Our customers expect reliability, and our team takes that personally,” said Jim Leach, Factory Manager. “We bring together advanced technology, smart processes, and the dedication of our people to assemble combines and front-end equipment that are tailored to each customer’s needs.”
That commitment—to our customers and our team—is exactly why we’ve made investments to take Harvester Works to the next level in manufacturing excellence.
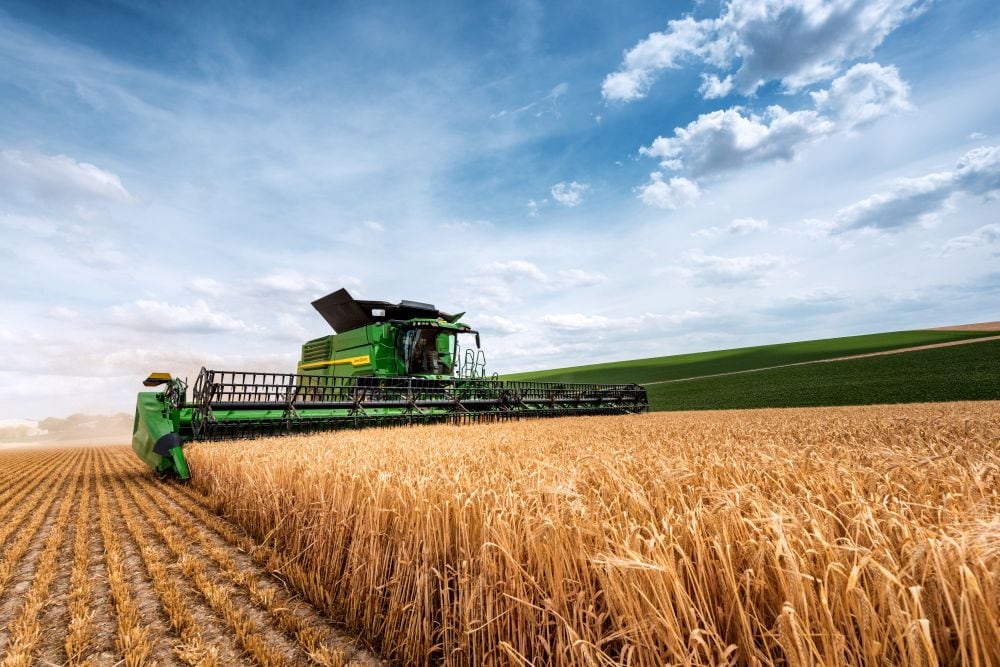
Welcome Home, X9
The X9 combine isn’t just our most advanced combine harvester, it’s a symbol of what’s possible when innovation meets purpose. Built for farmers who demand more capacity, more uptime, and more precision, the X9 reflects everything we’ve learned from over a century of product development and manufacturing.
“To assemble a machine like the X9, we had to think differently,” said Leach. “It meant investing in the tools, the technology, and the environment our people need to do their best work.”
That’s why we committed $48 million to renovate 385,000 square feet of manufacturing space at Harvester Works. And we didn’t stop there. We added another $101 million in cutting-edge equipment and processes to support the X9’s production, ensuring every machine meets the highest standards from the inside out.
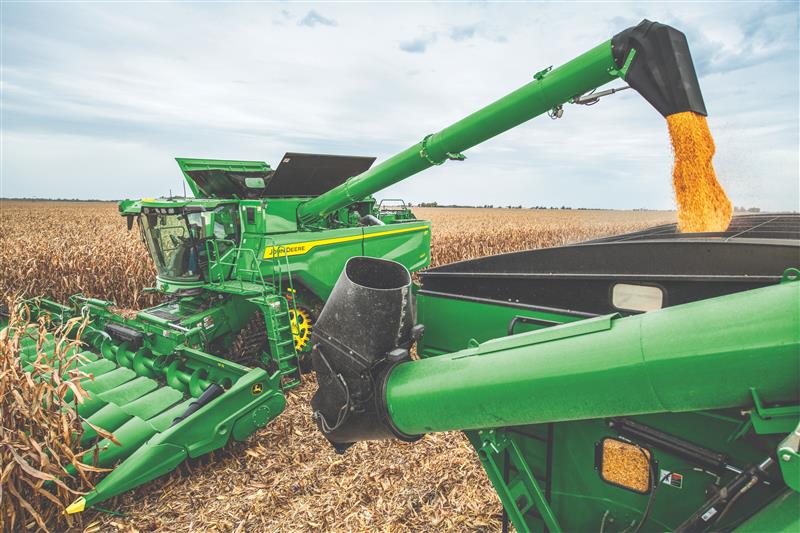
Unloading, Upgrading
To support one of the X9’s most critical features, we built a brand-new $13 million unloading auger fabrication cell. This dedicated space ensures precision, consistency, and quality.
“The unloading auger is a key part of the harvesting experience,” said Leach. “This new cell allows us to carry the manufacturing processes and quality enhancements originally from X9 onto the S7 product family.”
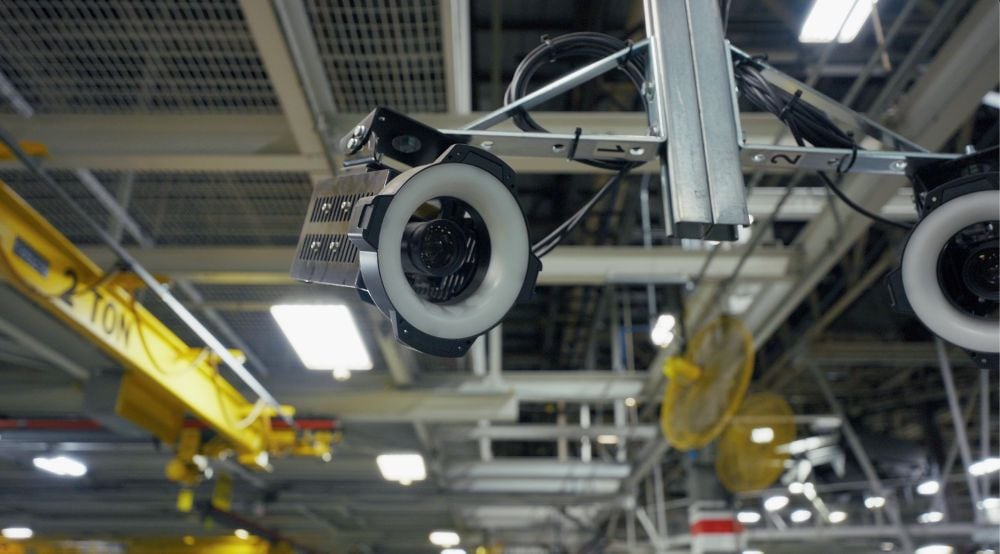
Advanced Cameras
With a separate $3.5 million investment, we’ve deployed more than 400 computer vision machine learning cameras across the factory. These cameras inspect around 2,500 unique items, helping us catch even the smallest problems before they become big issues.
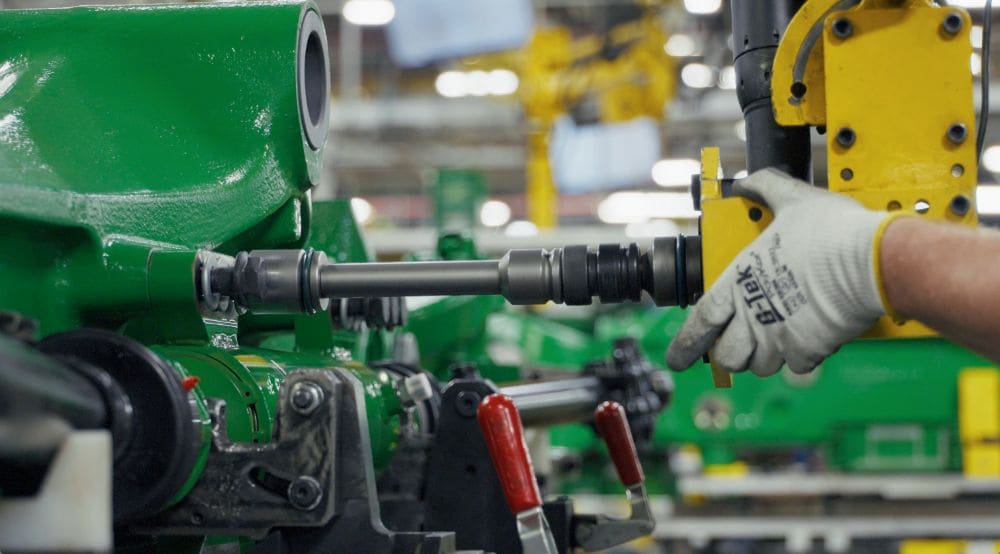
Tools That Think
Loose bolts? Not on our watch. We’ve added $4 million worth of high-tech torque tools that monitor torque and angle, lock out reverse motion, and stop the line if something’s off.
“Our goal is to assemble it right the first time,” said Leach. “These tools give our team the confidence and control to do exactly that.”
Our assembly line uses proprietary software that guides each step, tracks torque counts, and ensures the right parts go in the right place. If something’s not right, the system won’t let the machine move forward. That’s quality control in action.
Rooted in Community
Our commitment to community also runs deep – from investing in local students through hands-on programs like the Iowa High School Apprenticeship and Metal Inert Gas Weld Scholarships, to supporting veterans and local causes through donations and volunteerism.
“Our initiatives reflect our dedication to uplifting and supporting our community. We believe in making a meaningful difference in the lives of those around us,” Leach shared.
Looking Forward
These investments are just the beginning. Harvester Works isn’t going anywhere, and neither is our drive to keep improving. “As technology evolves and customer expectations grow, we’ll keep raising the bar right here in East Moline, delivering machines our customers depend on,” Leach concluded.
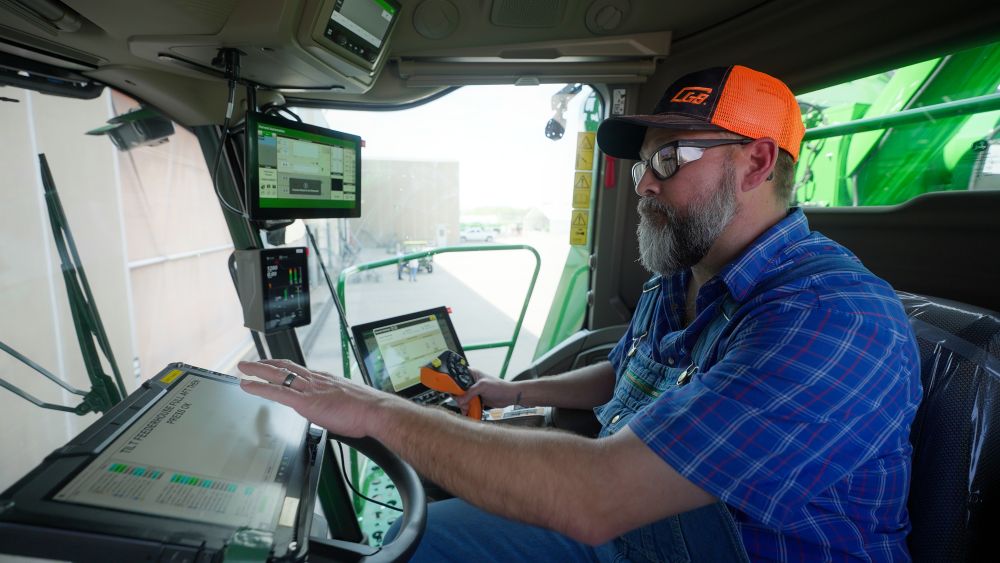